Asynchronous Open-Source DLX Processor (ASPIDA)
Implementation of the model
|
|
Figure 1
depicts a possible implementation of
the controller. Inputs P1 ...Pn are the L signals of its n
predecessor
controllers, while inputs S1
...Sm
are the L signals of its m
successor controllers.
considered. The delay element must have a delay for the
rising transition which is
larger than that of the combinational
block, while the falling transition delay determines the pulse width.
Such an asymmetric delay chain can be built easily with not
and nand gates.
Figure 1:
Implementation of the latch controller.
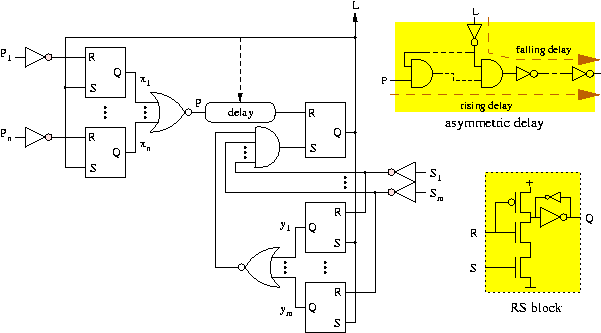 |
The sequence of events that determines the corresponding
delays is the following:
This is not the only way to implement these
controllers. The semi- and fully-decoupled controllers presented in
[4]
are also valid, although a formal proof of their
correctness in this context is more complicated. Similarly for the
controllers presented in [12,13,14].
Physical Design and Testing
Matched Delay Insertion. The flow that we used for the
de-synchronization approach
begins with a synthesizable HDL specification
(e.g. Verilog/VHDL), using the conventional synchronous HDL
constructs. Next, each datapath
element is synthesized for the target cycle time TT,
using a conventional synthesis tool.
Due to the load of the local clock by the registers of
the datapath block, buffers are inserted at this stage.
The circuit is analyzed using conventional static timing analysis
tools to estimate the delay of each matched
delay element. These matched delay elements are generated and
embedded into latch controllers. At this stage, the datapath blocks
and their corresponding latch controllers are combined to form the
complete netlist of the de-synchronized circuit. Once the complete
netlist is assembled, it may be simulated and its
correct operation verified using a gate-level simulator.
The circuit is then placed and routed, and the post-layout delays
are
extracted.
The pessimistic delays used for pre-layout timing analysis are now more
precise, and redundant not and nand gate pairs can
be
removed from the delay chains, by exploiting the incremental
place-and-route
capabilities of modern tools.
The possible modifications of different stages in conventional
automatic design flow for doing de-synchronization are shown
in Figure 2.
Figure 2:
Changes in the standard synchronous design flow.
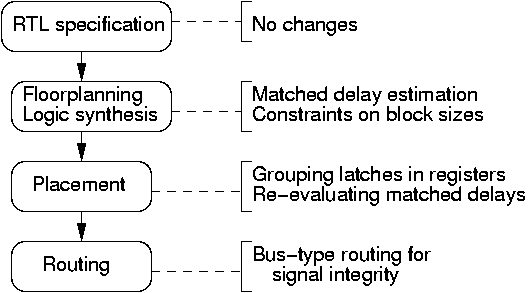 |
Design for Testability.
The datapath can be tested by using scan path insertion
with synchronous tools. A clock can be distributed to every register
and used only in test mode. Local
acknowledge wires in test mode allow one to build this network without
skew
problems. Thus it is considerably smaller than in the
synchronous case, where it must satisfy tight skew constraints.
Moreover, it is kept idle during normal operation.
Asynchronous handshake circuits can also be tested by using a
full-scan
methodology, as discussed in [11].
This has a performance and
area overhead, but it is essential for the acceptance of the
methodology. The goal is to ensure full coverage. Handshake circuits
are
self-checking, and
the work in [7]
showed that 100% stuck-at coverage can be
achieved for asynchronous pipelines using conventional test pattern
generation
tools.
De-Synchronization Case Study
Figure 10:
De-synchronized DLX.
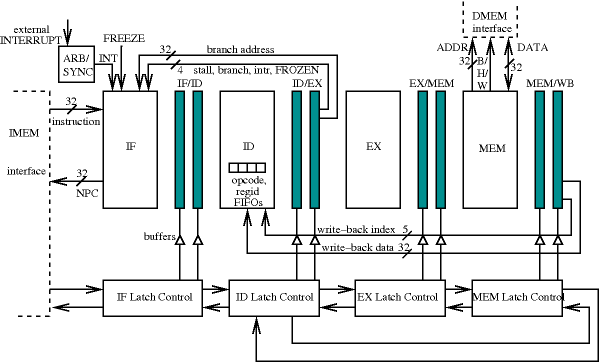 |
We present results on the application of
de-synchronization to a DLX processor.
The de-synchronized DLX consists of five architectural DLX pipeline
stages, four of which
actually correspond to circuit blocks (at the circuit level WB is
merged with
ID). Each block is controlled by its own latch controller. The arrows
of the latch controllers correspond to their and signals,
and illustrate the datapath dependencies. Stages ID, EX and MEM form a
ring. ID
is the heart of the processor containing the Register File and all
hazard-detection logic and synchronizes stages IF and MEM. Thus,
instructions
leaving MEM (for WB) will synchronize with instructions coming from IF.
This is
indeed necessary for handling data dependencies, as a register being
written
may be the same with the one needing to be read in a current
instruction.
Data hazard detection takes place by ID comparing the output register
of
instructions in other pipeline stages and their opcodes, and deciding
on
inserting the correct number of NOPs.
After the initial synthesis of each circuit block using latches,
the whole design is optimized incrementally to meet all timing
requirements.
Max-delay constraints between latches are used to ensure cycle time in
the datapaths but the control blocks are untouched inside G2C-RC, our
synthesis tool.
Then the gate-level netlist and matching timing constraints are
imported into SoC Encounter. Floor-planning is done along with
creation of power structures inside Encounter. All the standard cells
are placed using Amoeba and routed with
NanoRoute. Post-route optimization is iterated until all timing
violations are fixed. The synchronous DLX is obtained using the same
flow with
the additional step of Clock Tree Synthesis in Encounter before the
Route stage.
Table 1
contrasts the characteristics of the synchronous and
of the de-synchronized DLX.
The data are post-layout results based on
gate-level simulations with back-annotation of extracted parasitics.
Table 1:
Synchronous vs. De-Synchronized DLX.
|
Sync. DLX |
De-Sync. DLX |
Cycle Time |
4.4ns |
4.45ns |
Dyn. Power Cons. |
70.9mW |
71.2mW |
Area |
372,656 um² |
378,058 um² |
|
Figure 3:
FFT of current consumption in synchronous (above) and de-synchronized
(below) DLX
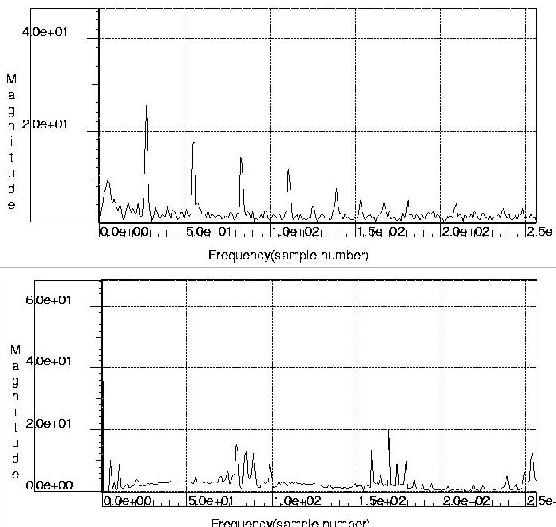 |
One can see that both designs have approximately the same area, speed
and power consumption. The Electro-Magnetic Emission cannot be
effectively
measured without fabricating the chip. However, we estimate the
advantages of
de-synchronization in this respect by measuring, with a power analysis
tool, the
waveform of the current absorbed by the circuit from the power rails.
Its
spectrum, shown in Figure 3
for the synchronous FF-based circuit
and the de-synchronized one
(the synchronous latch-based one had similar characteristics) shows
approximately 30% lower emission peaks in the desynchronized case,
which should
also be reflected in lower EMI.
Unfortunately about half of the circuit gates and flip-flops (due to
the
register file) is contained in the ID stage, which has a very complex
local
clock tree. This represents a worst-case for our methodology, since the
ID
stage is almost as noisy as the original synchronous circuit, but we
are still
able to show advantages with respect to a purely synchronous
implementation
in terms of estimated
Electro-Magnetic Emission.
|